“Standard industrial burners” refer to those combustion equipment widely used in the industrial field. They are significantly different from small burners such as civilian kitchen appliances and heating furnace burners used in the petrochemical industry.
The difference is that standard industrial burners are usually a series of standardized models designed based on specific heat load requirements, which can meet the precise control and efficient use of heat in different industrial processes.
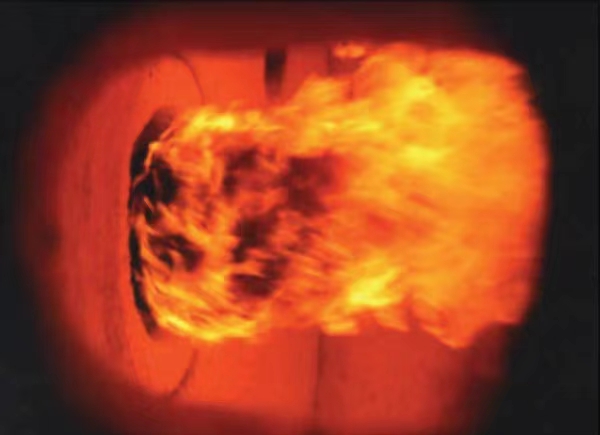
Standard Industrial Burner Control Systems
Widely used
These burners are widely used, covering a wide range of applications, from precision coating processes in the automotive industry, to efficient operation of direct-fired heating systems, to environmentally friendly treatment of volatile organic compounds (VOCs) waste gas, as well as waste incineration power generation, drying of various industrial products, high-temperature smelting in the glass manufacturing industry, and other key sectors.
In these complex and changing industrial application scenarios, standard industrial burners demonstrate their strong adaptability and high energy efficiency.
Diverse structures
The structural design of industrial burners reflects diversity to meet the combustion efficiency and safety requirements under different operating conditions.
From basic diffusion burners to fully premixed burners, the main brands include: Kromschroder, Maxon, Eclipse, Riello, Weishaupt, Baltur, Honeywell, etc.
The design structures of various brands of burners have their own characteristics, and each design is based on principles of thermodynamics and fluid mechanics, as well as precise engineering calculations, with a high degree of standardization
With self-control
A major feature of standard industrial burners is their integrated automation combustion control function, as well as their built-in fans.
This means that the burner not only has stable and reliable combustion capacity, but also can respond to complex control signal commands, achieve precise temperature control, fuel air ratio adjustment, and emergency shutdown protection functions.
The number of control functions depends on the requirements of the customer’s application scenario, some only have pressure detection and flame detection.
System composition
In addition to the burner body, it should also include: gas valve pipeline used to supply main fuel gas to the burner, including main gas shut-off valve (double valve), gas flow control valve (gas regulator), gas high and low pressure detection, leak detection switch, small fire pipeline shut-off valve, etc.
The gas valve pipeline has multiple safety detection and control functions, and can adjust the fuel output according to requirements.
The burner combustion fan is generally a centrifugal or medium pressure fan, and its air volume and pressure parameters should be able to overcome the resistance of the air duct and flue, provide the amount of combustion air required for normal fuel combustion, and have a certain overload operating capacity.
The detailed parameters of the fan need to be selected and determined based on the performance curve of the burner body.
The control cabinet is the control center of the burner system, which controls the entire process of burner startup, normal operation, load regulation, safety monitoring, and shutdown to ensure the safe operation of the system.
Specific control functions
By integrating the burner body, fan, valve group, and control cabinet, the entire process monitoring of the burner from start-up, operation to shutdown, as well as various safety interlock alarms, ensures the safe and reliable operation of the equipment.
The burner control system mainly includes three aspects: operation program control, output regulation control, and safety protection control.
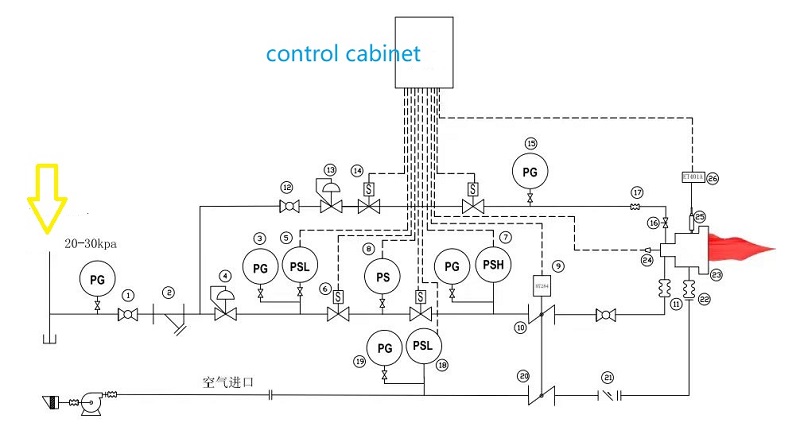
burner control systems
Program control operation
Under normal operation, the burner will operate according to a basic procedures: fan start-up – confirmation of process gas – valve proof gas leak detection – pilot ignition flame – main flame – normal combustion – normal shutdown – process gas blowing – shutdown.
If a safety interlock fault occurs during startup and operation, the control system will suspend operation by sending an alarm signal to lock the burner, the burner can be restarted after troubleshooting and resetting.
Output regulation control
After the equipment is running normally, the fuel output can be adjusted automatically or manually to meet the furnace temperature requirements.
When selecting the automatic mode, the system receives a furnace temperature signal to automatically drive the regulating mechanism, driving the fuel flow rate or synchronously changing the ratio of fuel and air flow rate to achieve the purpose of automatic control of flame size.
The manual mode is to manually force the drive to control the flame size.
Security protection control
Always monitor the operation of the equipment. Due to the flammability and explosiveness of gas, the safety performance of the combustion device must be a priority issue in the design scheme.
Sufficient safety devices should be installed and reasonable control should be carried out to ensure that the control system can not only meet the automatic control of the combustion process, but also basic safety protection needs, such as:
- Ignition condition judgment
- Automatic ignition
- Combustion status monitoring
- Ignition failure protection
- Shutdown protection
- Gas pressure high and low limit protection
- Insufficient combustion air pressure protection
- Power outage protection
- Prevention of gas internal leakage
To verify the relevant technical parameters and equipment operation status:
- When all parameters are normal, the burner will maintain normal combustion status.
- When certain parameters or states fail, the system will emit sound and light alarm signals to stop combustion or lock.
- When a lock occurs, it needs to be manually reset after troubleshooting to restart the burner
According to the combustion control requirements in the on-site furnace, safety control requirements are proposed for the burner, and the combustion control can have the following functions:
Confirmation of ignition conditions
- After power on, the gas pressure is within the high and low limit range
- The differential pressure switch of the combustion air meets the ignition requirements
- The furnace pressure (differential pressure) switch meets the ignition requirements
- Accept remote ignition instructions
Automatic ignition
Using a high-voltage ignition transformer to ignite the electrodes, with a voltage greater than 5000V
Combustion status monitoring
Accept the UV flame detection signal. Once the flame detection detects a shutdown state, the burner should enter a protective state and the gas supply must be immediately cut off.
Ignition failure protection
When gas is introduced into the ignition pipeline, the spark electrode starts to ignite.
If the flame cannot be detected by the flame detector within the safe ignition time, the gas solenoid valve should be cut off
Gas pressure high and low limit protection
The fuel gas of the burner must operate within a certain pressure range to ensure that combustion does not desorb, backfire, or stall
At the same time, limit the working power of the burner. If it exceeds the limit range, there should be more pressure development signals to cut off fuel supply and lock the burner in operation
Protection against insufficient combustion air pressure
The burner adopts forced air supply. If there is a fan failure or a huge fluctuation in furnace pressure, resulting in insufficient supply of combustion air, the gas should be immediately cut off to prevent accidents such as backfire or explosion.
Furnace pressure (difference) detection
Before ignition and during the operation of the burner, it is necessary to check the gas flow in the furnace to avoid dry burning of the burner or abnormal increase in pressure inside the furnace affecting the operation of the burner.
Power outage protection
If the burner suddenly loses power during operation, it should have the function of cutting off the gas supply.
Gas leakage detection
- Internal leakage controller combined with dual solenoid valves, check if both solenoid valves are working reliably and if there is any leakage.
- Before ignition, conduct a gas leak detection on the gas pipeline. If it does not meet the requirements, immediately lock the burner and stop working; The internal leakage controller is generally independent of the main program controller of the burner.
- The leakage detector detects a gas leak, and the signal is transmitted to the combustion controller. The gas supply should be cut off to stop the burner from working.
Reset
During the automatic operation of the burner, if a fault occurs and enters the locked state, the fault must be eliminated first before pressing the “reset” button to restart the burner.
Signal interaction between burner and host unit
- Signal from the upper computer to the burner: remote start/stop, burner reset, burner safety interlock, temperature control signal.
- The signals sent by the burner to the host unit include: burner operation signal, burner shutdown signal, burner air pressure low signal, natural gas internal leakage signal, natural gas high pressure signal, and natural gas low pressure signal
Summary
All the above functions need to be verified before the burner is shipped from factory, and corresponding debugging and operation settings should be carried out on the customer’s site