Description
What is an air heating burner ?
An air pheating burner is an air heat exchanger designed for commercial air heating applications.
A wide variety of applications– ranging from dryers and crop drying, paint spray booths, ceramic industry , as well as air replacement or air make-up air facilities, such as in distribution centres, factories, and warehouses, etc.
Feature & Advantages:
- Centred on a modular adaptable with square, rectangular or circular air ducts easily.
- Accurate temperature control, high turndown and low emissions
- Flexible designs enable fast response to changes in system temperature and air flow requirements.
- The adaptability meets the fundamental demand for flexibility found in a growing variety of application scenarios.
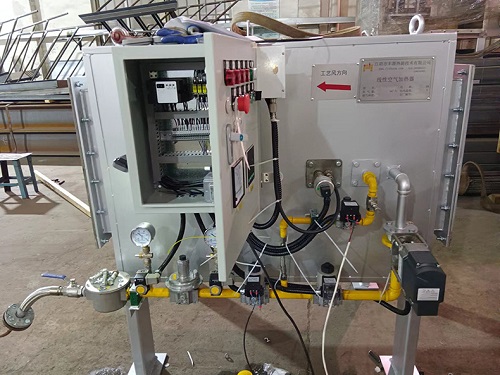
400,000 kcal ducted linear air heater, air heating gas burner
400,000 kcal linear gas burner air heater
With hot air stove adopting a pipeline type low-temperature direct combustion burner system:
- Heating medium: air (O₂% needs to be >17%, for supporting combustion)
- Medium inlet and outlet process temperature: inlet 15 ℃, outlet 250 ℃
- Medium flow rate: 6500 kg/h (reference data)
- Fuel type and calorific value: natural gas (uninterruptible), calorific value: 8500kcal/Nm³
- Inlet pressure of fuel access equipment: 35-45kPa, needs to be confirmed in advance, otherwise the user must bear the cost of replacing the pressure regulating devices.
- Operating environment temperature: -15℃-60℃
- Fuel inlet pipe diameter and flow rate: inlet pipe diameter – DN25, flow rate not less than 25Nm³/h;
- Voltage/phase/Frequency : Drive/control power 380V±10 % / 220V±10 % , 3-phase, 50 Hz± 5 %
Application
Food drying, chemical drying, metal heat treatment, waste gas/wastewater treatment, etc.
Based on comprehensive consideration of the process conditions, parameters, original equipment forms and other information provided by the customer, the hot blast furnace adopts a ducted combustion system.
Since the gas to be heated is normal air, there is no need to equip a combustion fan. The linear burner can directly utilize the oxygen in the air that needs to be added for combustion.
Model selection
According to the data provided by the customer, the burner power is designed to be 1.5 million kcal/h. This series adopts a modular design and can be assembled flexibly according to different power requirements and application scenarios.
This burner has good combustion quality and low NOx emission levels. The combustion is in a linear state, and the temperature distribution is more uniform than conventional combustion methods.
This linear burner is usually installed directly in the air duct and is suitable as an alternative to traditional hot air stoves with low outlet air temperatures. It has the advantages of space saving, low investment cost, and good combustion effect.
Valve assemblies
Choose professional combustion brand valves, such as German SIEMENS, German DUNGS, German KROM, etc., which are the most reliable in terms of safety, professionalism and quality.
Valve functions include: manual cut-off valve, gas high and low pressure display and pressure safety interlock switch, double cut-off solenoid valve, automatic flow adjustment valve( gas regulator ), etc. It is also equipped with an independent ignition pipeline to ensure ignition cost efficiency and stability.
Control systems
The system uses a MAC temperature controller to perform PID control of the burner power. Under rated power, the temperature control accuracy reaches ±2°C.
The system has emergency stop, automatic alarm, alarm safety lock, continuous flame signal detection and other practical functions to ensure that the hot blast stove works stably with reliable performance, improved usability and ease of maintenance.
- Pre-start conditions: the rear induced draft fan and post-processing equipment have been started
- Step 1: start the air blower, then start the main induced draft fan, differential pressure switch closed
- Step 2: Start the ignition program and the program controller starts working
- Step 3: Ignition transformer starts to discharge, ignition solenoid valve opens, high-voltage ignition electrode sparks, ignition successful, and the flame detector detects the flame
- Step 4: The main gas valve open and the main flame forms. After the main flame is stable, the small fire valve is closed and the furnace heats up
- Step 5: According to the temperature measured by the thermocouple, adjust the opening of the main gas pipe regulating valve in real time to ensure the outlet air temperature and the system enters a stable operating state
Safety instructions: (System abnormal cut-off time <1s)
The hot blast stove has gas pressure monitoring function, gas low pressure monitoring and gas high pressure monitoring, and the monitoring values can be set.
Gas low pressure monitoring: When the gas pressure is lower than the set value, the burner will automatically stop working. Gas high pressure monitoring: When the gas pressure is higher than the set value, the burner will stop working.
The burner has a flame monitoring function. When the flame detector is powered on, it can monitor the furnace flame in real time 24 hours a day. Under normal combustion conditions, the burner will stop working once the flame signal is lost. When the burner is stopped, if the flame detector detects a flame signal, the combustion program controller will issue an alarm.
The burner has a pre-start purge function and a post-stop or alarm purge function. After the burner is started, the time between successful ignition is pre-ignition purge. After the burner stops or alarms, the time for the combustion program controller to move from the current position to the initial position is the burner post-purge time.
The burner has burner failure and over-temperature alarm functions. The power distribution cabinets are equipped with alarm indicators (sound and light alarm at the same time), and the alarm temperature can be set to the temperature required by the user.
The burner has double emergency cut-off valves: Once the burner stops working or malfunctions, the double valves will immediately shut off the gas in the gas pipeline to prevent gas from leaking into the furnace. Double valves can achieve safer protection.
The electric control cabinet is equipped with an emergency stop button. Once an emergency occurs, the burner can be stopped immediately to ensure safety accidents.